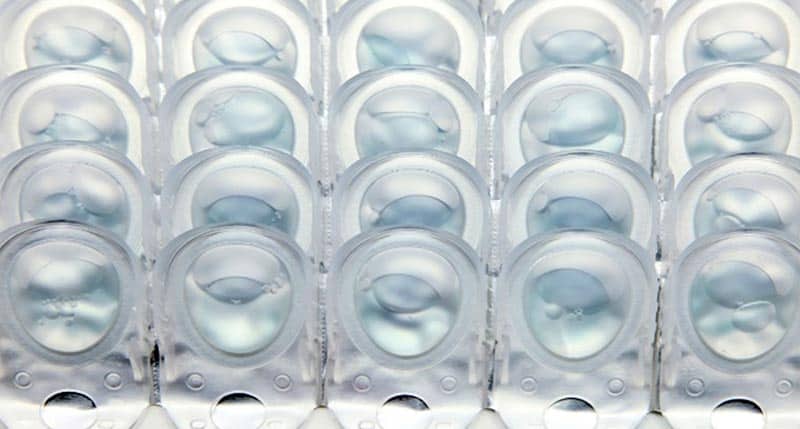
06 Apr How Contact Lenses Are Made
If you yourself don’t wear them, you almost definitely know someone who does: Contact lenses — those small, curved pieces of plastic that correct vision impairment — are one of the most successful medical device technologies. They are a part of daily life for millions of Americans. But how were these clever lenses developed, and how are they made?
Contact lenses are corrective or cosmetic devices worn on the eye, typically made of thin plastic that sits atop a layer of tears over the cornea. For many of our patients, especially athletes and those with an active lifestyle, they are the preferred vision correction method over glasses because they offer convenience and freedom of movement.
There are three main types of contact lenses in use today: soft, gas-permeable, and hybrid. Soft lenses are the most comfortable because they have the highest water content. The downside is that the thin plastic can rip very easily. If you wear daily lenses, you wear soft lenses. Hard or gas-permeable lenses are another option that offers the best vision correction for specific eye shapes or vision conditions. While these can last for years (if you don’t lose or crack one), they can “pop” out of the eye, and their rigid nature can require an adjustment period before they feel comfortable. There is a third type – a compromise between hard and soft lenses: Hybrid lenses feature a rigid plastic center surrounded by a softer “skirt” of plastic at the edges. They offer the crisp vision of a hard lens with the increased comfort of a soft lens.
History of Contact Lenses
Long before today’s plastic technologies existed, the first contact lens was developed by German physiologist Adolf Fick in 1887. It was made of glass and covered the entire white part of the eye, known as the sclera. Other scientists developed corneal and scleral lenses made of Plexiglas and plastic, but fitting them required an uncomfortable process of creating an impression of the eye (ouch!).
The first successful soft contact lenses were developed in Czechoslovakia in 1954, made of a hydrophilic gel polymer plastic that was comfortable enough to wear in the eye. Despite initial scorn from the optics community, Czech scientist Otto Wichterle persisted in perfecting soft contact lenses in his kitchen. He and his wife eventually produced thousands of pairs for testing.
The raw material for contact lenses is a plastic polymer, with hard lenses typically made of polymethyl methacrylate (PMMA) and soft lenses made of poly hydroxyethyl methacrylate (pHEMA) or other hydrophilic materials. Hydrophilic means “water-loving,” so it absorbs and mixes well with water and the tear layer of your eyes. Lens manufacturers continue to make advances in materials that will provide the best vision and comfort. While most contact lenses are worn during the day and removed at night for cleaning, extended-wear and daily wear lenses are also available for added convenience.
How contact lenses are made
Contact lenses are made from a variety of materials, each with its unique properties. The modern manufacturing process involves 7 steps.
- Lens Shape and Design. Manufacturers must first design a contact lens that meets the specifications of the prescription. This process is based on factors such as the degree of refractive error, pupil position, and eye shape. Special design software enables precise calculations and adjustments.
- Lens Material. There are various lens materials available for contact lenses, including soft hydrogels, silicone hydrogels, and rigid gas-permeable materials. The ideal material is selected based on prescription strength, oxygen permeability level, and wearer comfort.
- Lens Molding. The lens molding process shapes the lens material according to design specifications. Using specialized, automated machinery, manufacturers can produce very precise and intricate shapes to accommodate the unique eye shape of each wearer.
- Lens Casting. The plastic lens material is heated until it is soft and pliable, then injected into the lens mold, where it is pressed into the correct shape. The lens is then cooled to set its shape.
- Lens Cutting. The lens-cutting process is a precision, typically automated operation with careful attention to detail to ensure that the lens is cut to the exact design specifications for the prescription.
- Lens Finishing. Finishing involves smoothing and polishing the lens surface to remove any rough edges or imperfections to ensure it is smooth and comfortable for the wearer.
- Lens Inspection and Packaging. Contact lenses undergo a rigorous inspection process to ensure they meet the highest optical clarity and precision. Then they are packaged in a sterile container that keeps the lenses clean and safe during shipping and storage.
The end result is a high-quality lens that provides the wearer with clear and accurate vision!
Are You Contact-Curious? Call Us Today
If you or a loved one are curious about contact lens options, call us today to make an appointment. We will discuss and recommend the best contact lens options for your unique eye shape, vision impairment, and lifestyle needs. We’re excited to help you on your journey toward enjoying the freedom of vision that contact lenses can provide for your active lifestyle.
Sorry, the comment form is closed at this time.